Meaning of Prilling
The Main Principles of the Prilling Process and the Definition of a Prill.
Prilling is an extremely effective finishing technology and offers many advantages over other solidification methods. But what is prilling? And what is a prill? To define prilling, we need to examine both the main principles of the process and the end product. But before we do this, let's go back to where it all started...
Invention of Prilling
Legend has it that one night in 1782, William Watts, a plumber from the city of Bristol in the UK, was walking home after a night of drinking ale in the local pub. Along the way, he decided to take a rest near the St Mary Redcliffe Church, the lead roof of which he had recently renovated. As he lay on a bench, worrying about his wife’s disappointment alone home alone, he drifted off into a dream-filled sleep.
In his dreams, his wife's anger kept haunting him. He saw her towering over the church and, in her anger, she poured molten lead down the tower onto his face. The lead didn't form a stream but instead shaped into perfect spherical balls. He woke up to find that it was only the Bristol rain falling from the sky.
The next day he decided to experiment and, together with his wife, climbed the spiral stairs up to the church’s roof. They drilled holes in the bottom of a pan, melted some lead, and fed it through the holes. Just like in the dream, the molten lead formed spherical droplets, which solidified into perfectly spherical (definition of prill) lead balls before hitting the ground. These balls became known as patent lead shot, which was used in shotguns designated for hunting [1].
Previously, lead shot was produced according to a slow and laborious molding process, giving irregularly shaped and expensive lead balls. Watts, a keen hunter himself, was so convinced of this production method that he decided to build the world’s first prilling tower, right on top of his house [2].
Until this day, spherical products from the chemical industry are produced in very much the same way as it was invented by William Watts; currently known as the process of prilling.
What is Prilling?
Prilling is a shaping or finishing technology which is widely applied in the chemical industry. The process of prilling physically changes a molten stream of a product into solidified spherical particles, called prills, with a size between 500 and 4000 micrometers. In general, the prilling process consists of three main components; The prilling machine, the prilling tower, and the cooling medium.
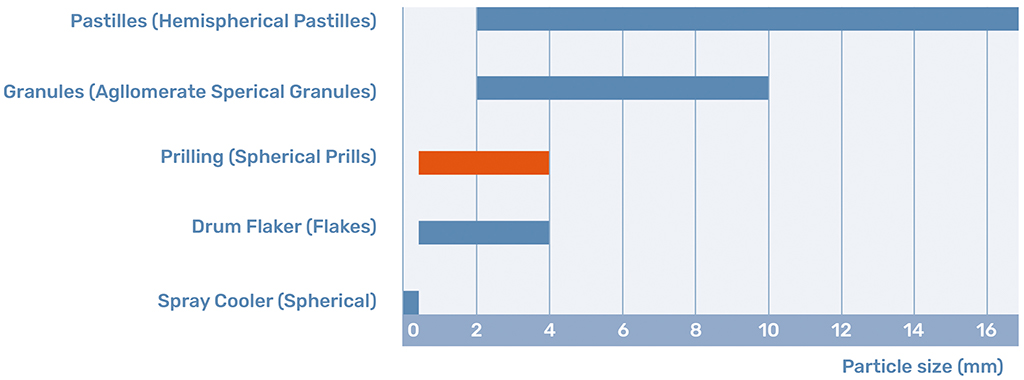
Prilling Machine
The prilling machine is the location where the prill is formed. The melt is formed in a jet by the prilling machine, which subsequently breaks up into droplets. The droplets that are produced solidify into the prills.
The formation and breakup of a liquid jet are governed by the physical properties of the melt. Therefore, each new prilling facility has to be designed in accordance with the material that needs to be prilled and the customer’s preferred size of the produced prill.
Prilling Tower
The droplets formed by the prilling machine solidify in the prilling tower. A prilling tower is operated with a gas stream of the cooling medium to cool the prills. The gas stream can be operated in two different ways; a countercurrent or co-current flow. The most common is the countercurrent flow since this operation allows the residence time of the prills in the tower to be increased and also gives better heat distribution over the tower.
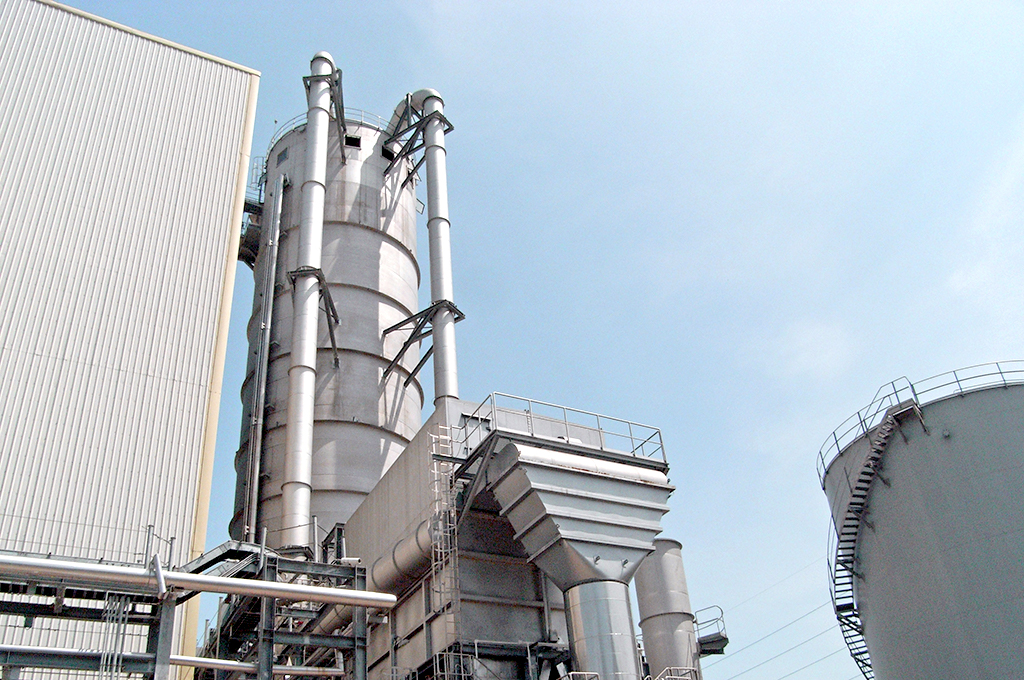
The different melts and the different particle sizes that are prilled require different tower heights to make sure the droplets are completely solidified before they hit the bottom of the prilling tower. Prilling towers can be everything from 20m up to more than 60m in height and are usually constructed from either cement or steel, depending on the melt and how corrosive it is.
At the bottom of the tower, the prills need to be collected and sent to packaging. A scraper is placed at the bottom, which gently pushes the prills to a screw conveyor that transports the product to big bags.
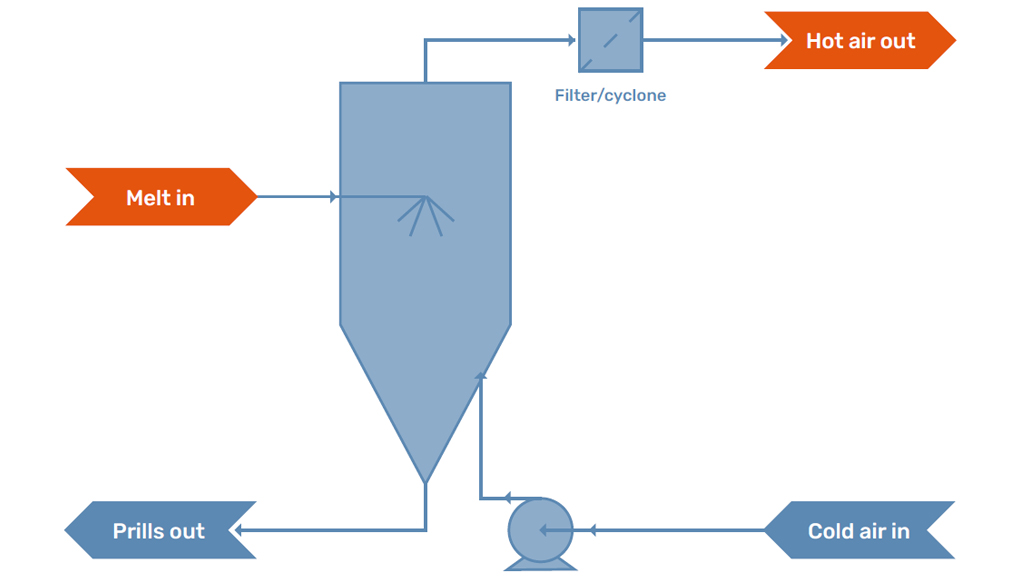
Cooling Medium
In the prilling tower, the droplets formed by the prilling machine are in contact with the cooling medium. Traditionally, prilling towers operate with an airstream in order to cool and solidify the prills. The air stream is either caused by natural draft, as a temperature difference will develop over the tower, or is influenced by a fan which creates and controls the flow.
There is always some dust formation inside a prilling tower. This formation can be due to evaporation, satellite droplets, or because parts of the prills break off on impact with the floor. Modern prilling towers are therefore equipped with a filter package to capture the formed dust and either reuse it in the process or package it as a separate product stream.
Next to the traditional air prilling towers, recent innovations have made it possible to use other cooling media, such as nitrogen, in the prilling process. This innovation is known as closed-loop operation and allows the cooling medium to be reused in the prilling process, eliminating dust emission into the environment.
The use of nitrogen ensures safe prilling of a whole new range of molten products, which are highly sensitive to dust explosions. This hazard was one of the reasons why the prilling industry stopped producing sulfur prills. Research at Kreber has shown that with our current innovations, this will possibly change in the near future. For more information about our most recent developments, please read the following article: sulfur formation and solidification technologies.
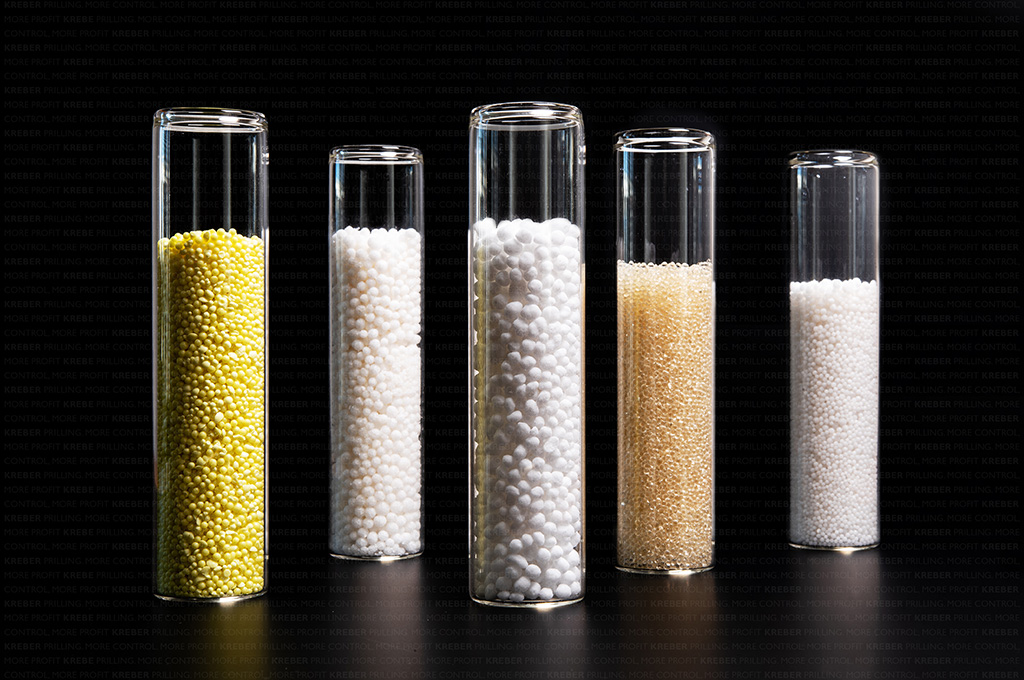
What are Prills?
Prills are the product of the prilling process. Prills are defined by their spherical shape and their size between 0.5 and 4 mm. This shape and size determine that the prill is a free-flowing product with certain distinct benefits.
The spherical shape of prill is preferred when a product needs to be free-flowing. A prill on a slightly inclined surface will already start rolling, making it easy to handle as a product. The size yields a product that is easily dosed but is not a dusty product, limiting product losses and maintenance costs.
Prills are widely applied in the fertilizer industry, as the size enables farmers to mechanically distribute them evenly over the soil. In addition, products with a high dust explosion risk are finished into a prill to limit that risk, as prills are larger than dust (< 500 mu). This is the case in BPA prilling, for instance.
Future of prilling
Even though prilling has been around for centuries, it is still evolving. While prilling was already a good choice for any market wanting a robust finishing method for their material, new innovations are in the works to improve and streamline the process even further.
An excellent example of a new innovation in prilling is a closed-loop system, where the cooling gas is reused after leaving the tower. Environmental emissions are reduced to practically zero and the safety of the operational process is significantly increased. Upcoming developments are the mitigation of the satellite droplet formation, which will also optimize the prill size distribution. These innovations make the prilling process a better alternative, compared to the other main finishing methods.
Major Benefits
Prilling is often the most preferred method because it offers the following advantages over other solidification methods:
- Most Cost-Effective
Prilling is one of the most economical finishing technologies in the world for large outputs. Compared with other solidification methods such as granulation and pastillation, CAPEX and OPEX are several times lower at increased capacities. - Highly Flexible
Prilling production is easily scalable within the range of 70 to 110% of the originally designed capacity. This makes the prilling production method an extremely flexible option for your total production process. The prilling process is also easily scalable in its throughput, making it an interesting alternative for companies looking for small batch - Guaranteed Continuity
The high degree of ‘self-control’ makes prilling a robust finishing technology with a very stable processing procedure. It can therefore play a vital role in guaranteeing the continuity of your process and quality of your product. - Energy-Efficient
The process requires minimal energy consumption. In fact, it is the most energy-efficient solidification technology available. This helps you minimize your operational expenses. - Convenient Operation
Our equipment is easy to operate thanks to our well-defined process operating parameters. Furthermore, the limited rotation and intricate parts result in a reliable process, giving the client low overall operational and maintenance costs. - Small Footprint
With the design of our prilling tower and additional equipment, you benefit from a relatively small footprint in comparison to other solidification technologies. - Emission-Compliant
Thanks to a constant stream of technical innovations, such as state-of-the-art air inlet filtration and scrubber technologies, prilling has evolved into a cleaner finishing technology than it has ever been.
References
- Harrison, David. Dream Lead to Invention. Bristol Times, November 26, 2002.
- Watts, Williams. Small Shot. 1347 United Kingdom, December 10, 1782.