Prills: unique characteristics and advantages
Prills are grains of solid substances formed from molten drops. The result? A free flowing product with low dust and a narrow particle size distribution.
Prills are spherical and naturally resistant to abrasion or damage. Since no additives are necessary in the prilling process, prills of your product are 100% pure.
Thanks to their size and shape, prills have the smallest possible contact surface area and high bulk density. In bulk, prills behave like a fluid which is beneficial for transport, storage and further processing.
This is why prills offer the ideal form of solidification for a wide range of substances and markets.
Looking for more information about the main principles of prilling? Please read the following article: prilling meaning and prill definition.
Prills for bulk properties offer you significant advantages:
- Excellent 'free flowing' properties
- Low tendency to stick and agglomerate
- Distinguished for air lifting
- Highly resistant to abrasion or damage
- Minimal dust formation
- Well suited for transportation in road tankers, containers and big bags
- Excellently storable in silo installations
- Precise dosage
- No additives needed; pure materials
Prilling: more control, more profit
Prilling is a extremely effective finishing technology and offers you the following advantages over other solidification methods:
Prilling is one of the most economical finishing technologies in the world for large outputs. Compared with other solidification methods such as granulation and pastillation, CAPEX and OPEX will be multiple times lower at increased capacities.
Our equipment is easy to operate, due to our well defined process operating parameters. Furthermore, the low amount of rotating and intricate parts result in a reliable process, giving the client an overall low operational and maintenance cost.
Prilling production is easily scalable within the range of 70 to 110% of the original designed capacity. This makes the prilling production method an extremely flexible option for your total production process. Quickly adapt to changes in the market? With prilling you can.
With the design of our prilling tower and additional equipment, you benefit from a relatively small footprint, compared to other solidification technologies.
The high degree of ‘self-control’ makes it a robust finishing technology with a very stable processing procedure. It can therefore play a vital role in guaranteeing the continuity of your process and quality of your product.
Thanks to a constant stream of technical innovations, such as state-of-the-art air inlet filtration and scrubber technologies, prilling has evolved into a cleaner finishing technology than it has ever been.
Unique oppurtunity: Pilot-Scale Test
Try It With Your Own Product
Wondering if Prilling is suitable for your material? Our specialized R&D team and laboratory offers you the unique opportunity to make a test batch Prills of your product, tailored to your application.
Lab-Scale Feasibility Tests:
Your substance is tested on prillability
Pilot-Scale Production:
If feasible, we produce a batch to simulate industrial performance..
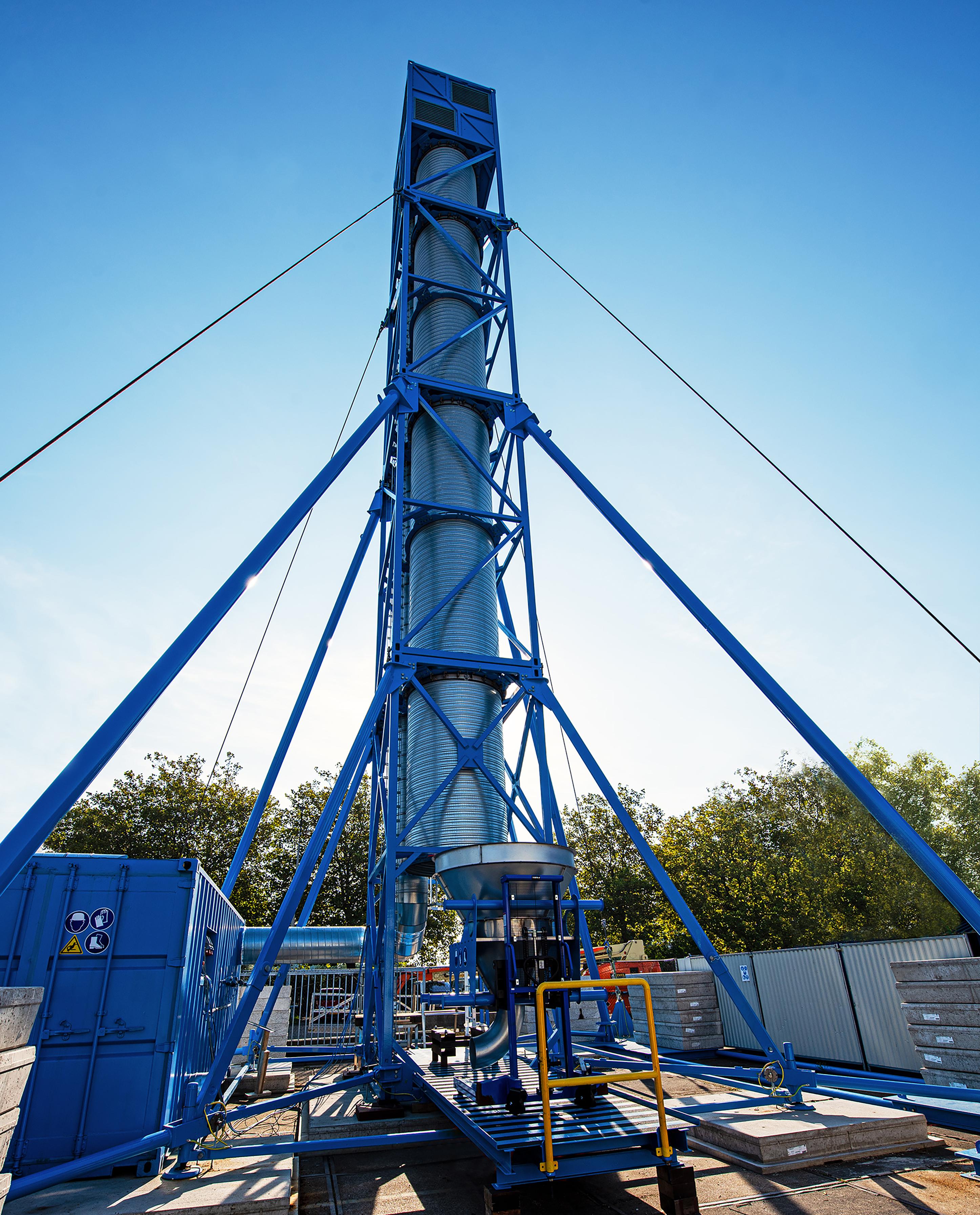