Grinding
In the realm of particle technologies, size reduction of solids plays a crucial role in transforming raw materials into refined products with improved properties.
This process involves reducing the size of solid materials to enhance their functionality, facilitate handling, and enable further processing. Among the various techniques used for size reduction, grinding stands as a cornerstone, offering unparalleled precision and versatility.
Understanding Size Reduction
Size reduction is the process of reducing the dimensions of solid materials, resulting in smaller particles or pieces. It encompasses a wide range of operations, including grinding, crushing, milling, cutting, shredding, and more. By breaking down solids into smaller sizes, size reduction facilitates better material handling, increases surface area for efficient reactions, improves uniformity, and enables the extraction of valuable components.
The Role of Grinding in Size Reduction
Grinding, one of the primary methods of size reduction, involves the application of mechanical forces to break down materials into smaller particles. This process utilizes grinding media, such as balls, rods, or abrasive grains, to physically impact, compress, or shear the solid material, resulting in size reduction. The Kreber grinder offers options to break up using mechanical force or knives to reduce the size of the products into a set size and shape.
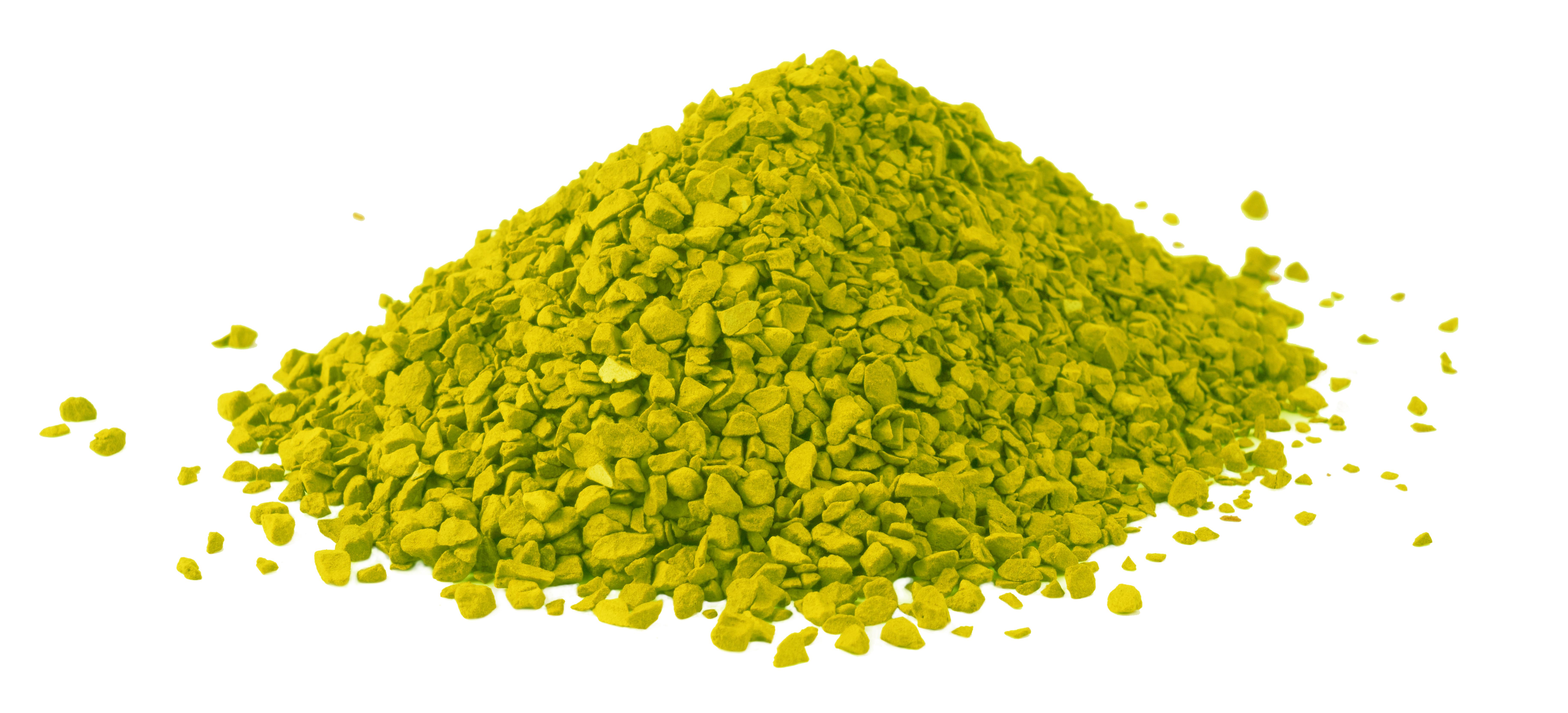
Smaller particles are easier to handle and move around. Grinding makes materials more manageable for transportation and mixing.
Grinding increases the surface area of materials, allowing for faster and more efficient reactions, like chemical reactions or dissolution.
Grinding helps achieve a more uniform particle size distribution, ensuring consistency in the final product.
Grinding can help extract valuable components from solid materials, like minerals from ore or precious metals.
Grinding works with a wide range of materials and allows precise control over the final size, shape, and distribution of particles.
Grinding is a cost-effective method compared to other techniques. It requires less energy and equipment, making it economically viable. By using grinding to reduce the size of materials, we can create refined products with improved properties in various industries such as mining&minerals, food, pharma, chemical & recycling processes.
One of the ways to define yield is by the fraction of the solute in the feed that is ending up in the final product. The fraction of solute in the feed that remains in the solution can then be considered as the loss.
The crystal structure, size, shape and purity can be used to express the particle product quality of a crystalline product. Customer and manufacturer specification for a crystalline product can usually be related to these four product quality aspects.
The crystal structure for instance impacts properties such as solubility, shelf life and bioavailability of a pharmaceutical compound. A crystal size distribution gives information on the collection of crystal sizes in the product, which is for instance an important parameter in determining the dissolution behavior of fertilizers and pharmaceuticals.
The crystal shape can be vital for flow and storage properties of a product. In the food, pharmaceutical and fine chemical industries high levels of purity are desired. For instance, impurities from side reactions during the synthesis of an active pharmaceutical ingredient could lead to unwanted additional biological activity of the administered drug if they end up in the final product.
Analytical techniques can be employed to measure and control particle product aspects throughout the manufacturing process.
Process parameters have a strong impact on the particle product quality. By understanding the relationship between process parameters and particle characteristics, manufacturers can optimize their processes to consistently produce high-quality particle products.
A higher supersaturation during a crystallization process might for instance lead to a larger nucleation rate and therefore more particles and a product with a smaller average size. However, a higher supersaturation speeds up crystallization, increasing productivity.
MicroPrilling Units
The Kreber MicroPriller is an all-in-one solution for transforming molten materials into solid powders with enhanced functional characteristics, including increased solubility or encapsulation of active ingredients.
Operating from a melt-in to powder-out battery limit, the Kreber MicroPrillers handle all necessary processes within the equipment itself, such as cooling, emission treatment, and reintroduction of the cooling medium (e.g., air, nitrogen, or other gases). This closed-loop configuration ensures near-zero emissions to the environment. Our MicroPrilling equipment is designed to be flexible, low-maintenance, and scalable, supporting capacities of up to 15 tons per hour.
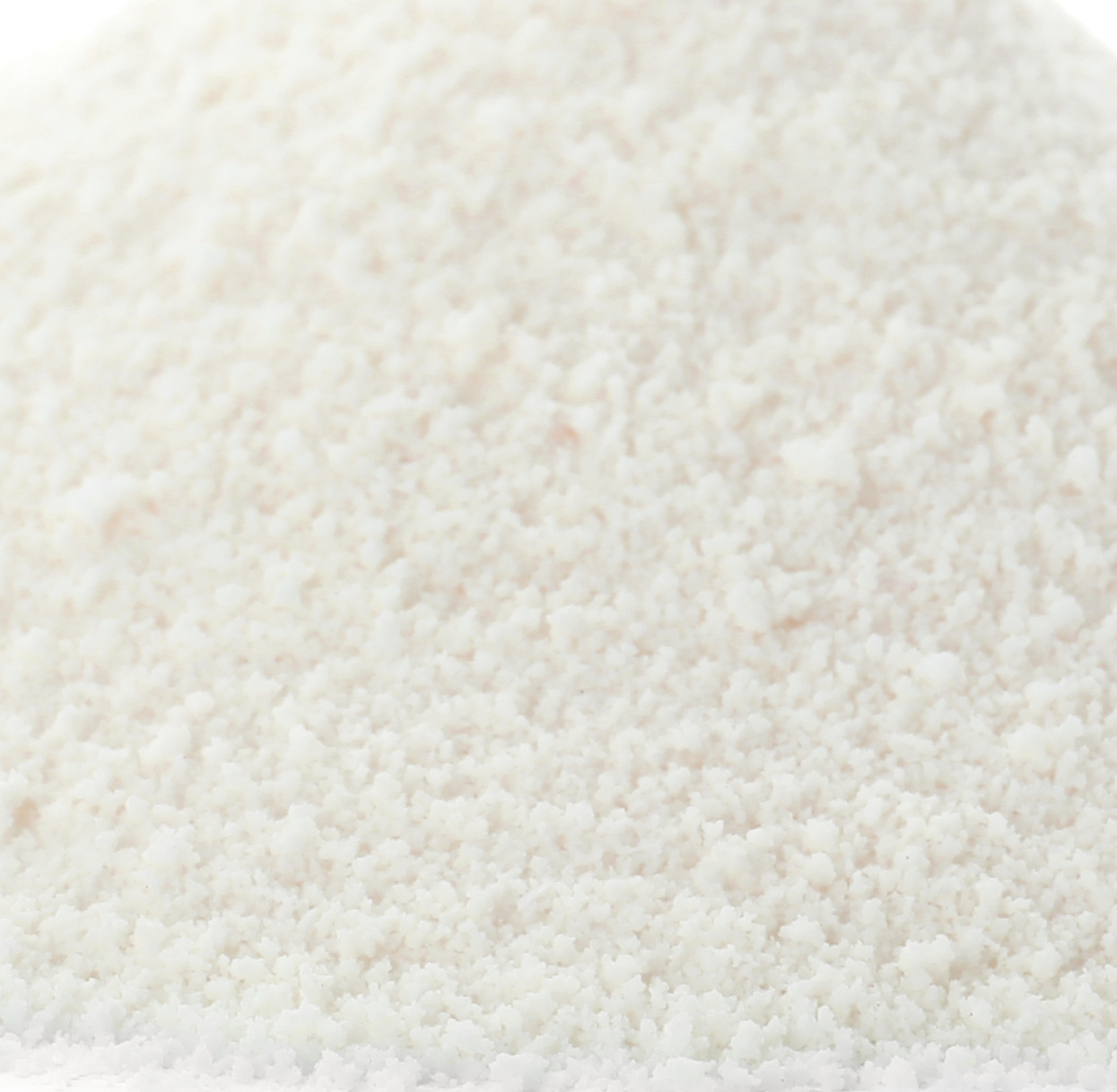
Full Package Overview
An overview of our full package for a Spray congealing unit
Atomizer
The atomizer nozzle breaks up the melt or slurry in small pre-defined droplets.
Cooling chamber
Inside the cooling chamber the droplets are contacted with a co-current gas cooling stream, allowing for rapid solidification.
Powder collection
The product is caught in a product cyclone, allowing for easy collection of the powder.
Bag filter
A bag filtering section is used to clean up any remaining particles from the air stream.
Heat exchanger
Just prior to re-introduction in the spray chamber, the cooling medium is cooled back to its operational temperature, allowing for closed loop operation.
Special options
Special options include ATEX equipment, encapsulation options, different cooling media.
Particle Technologies
Particle technologies are process technologies that produce, use, or separate particles.
For example, pharmaceutical industry produces precise drug formulations based on particle technologies. Activated carbon particles are commonly used in the food industry as an adsorbent to remove impurities, off-flavours, and odours from liquids such as water, beverages, and food ingredients. Chemical industries may use particles as adsorbents to remove certain components in separation processes. One example of separating particles in the chemical industry is the use of cyclones, which employ centrifugal force to separate solid particles from gas or liquid streams based on their particle size and density.
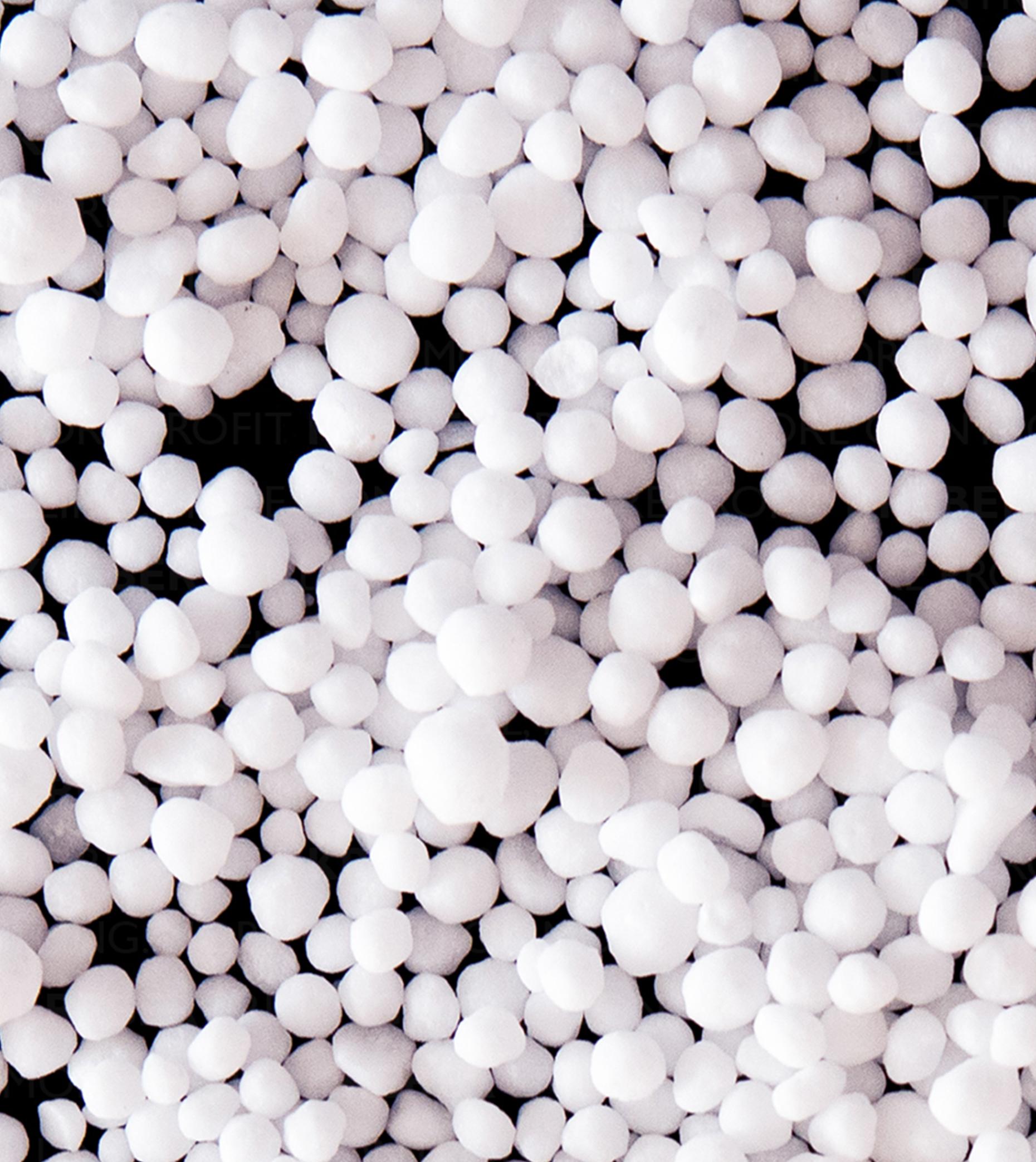
Particle Technologies
The technologies that produce particles can be divided into solidification, crystallization, and particle modification processes.
Spray Congealing
Spray congealing is an efficient process utilized in the manufacturing industry for the production of solid powders. This innovative technique involves atomization, rapid cooling, and solidification to create uniform and high-quality solid materials.
Atomization
The spray congealing process begins with the precise atomization of the liquid material. The liquid is heated to a specific temperature and then transformed into fine droplets using a high-pressure nozzle system. This atomization stage ensures that the liquid is converted into small, uniformly-sized droplets, setting the foundation for consistent particle formation.
Rapid Cooling and Solidification
The atomized droplets are introduced into a controlled environment, typically a temperature-controlled chamber. Within this chamber, the droplets come into contact with a cold gas stream or a cooling medium. The sudden exposure to the cool environment leads to rapid cooling and solidification of the droplets, transforming them into solid particles. The resulting particles exhibit spherical shapes, and uniform sizes.
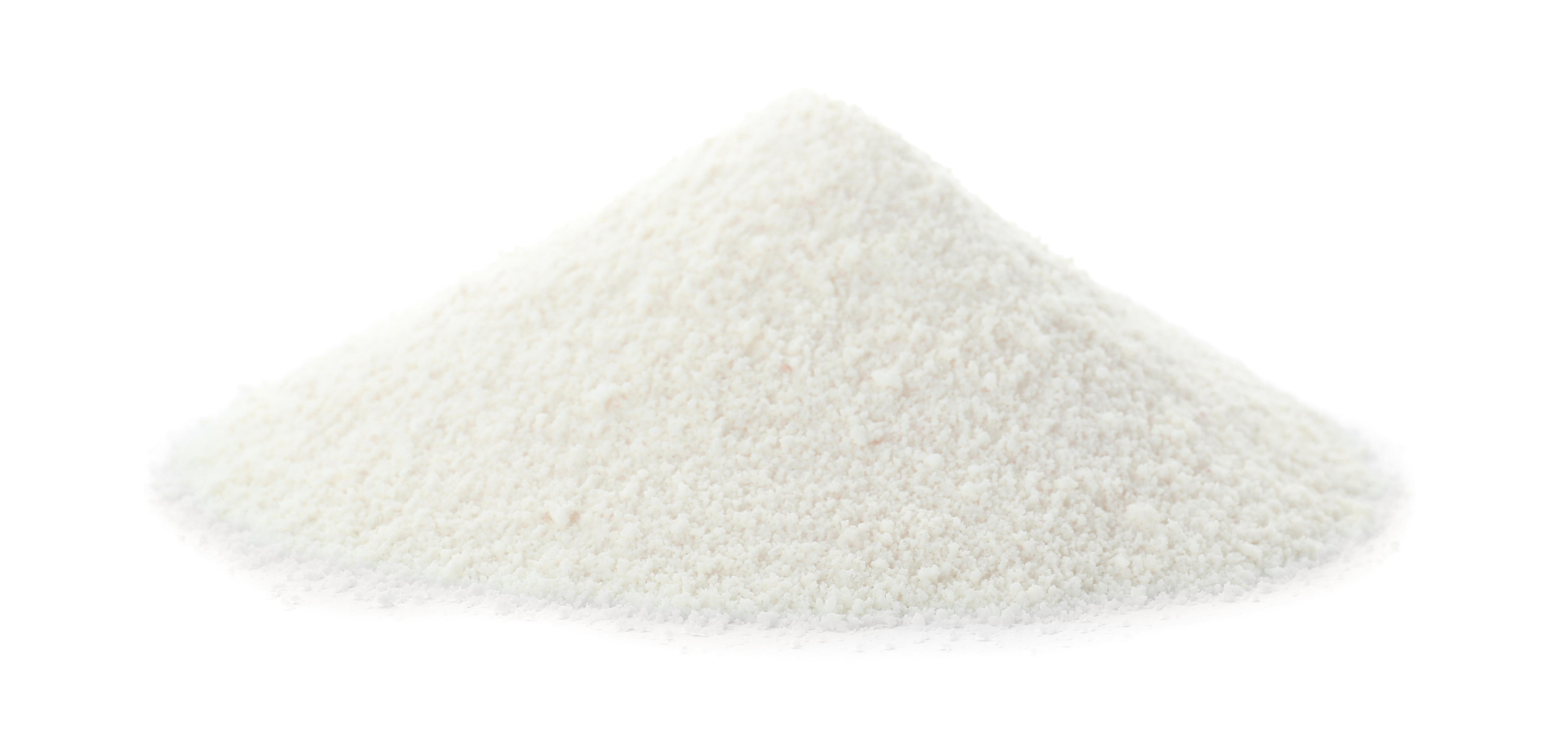
Spray congealing enables the production of spherical particles with precise and uniform sizes. This uniformity enhances product quality and performance, making spray congealing ideal for applications where consistency is critical.
Our equipment is easy to operate, due to our well defined process operating parameters. Furthermore, the low amount of rotating and intricate parts result in a reliable process, giving the client an overall low operational and maintenance cost.
The process is particularly advantageous for encapsulating sensitive or volatile substances. By solidifying the liquid droplets quickly, spray congealing can protect and preserve the integrity of sensitive components during the manufacturing process.
Spray congealing allows for the incorporation of multiple ingredients into compounded particles, facilitating the creation of composite materials with tailored properties. This flexibility enables the development of advanced materials with enhanced functionalities.
Thanks to a constant stream of technical innovations, such as state-of-the-art air inlet filtration and closed loop operation, emissions can be cut to virtually non existing.